The melt layer is sort of thin; for example, when cladding an aluminum alloy it's about 0.5–fourμm (Kreye 1985, 1997 ). The dilution of the molten zones leads to plane or corrugated interfaces. During mechanical decladding, the fuel assemblies are chopped and the gasoline core is leached with nitric acid, leaving behind the undissolved cladding materials for disposal as a strong waste.
Hydrogen addition in boiling water situations just isn't very efficient as a result of segregation of hydrogen within the steam section. The interplay that fuel cladding tubes experience as a result of fission merchandise on the inner surface is stress corrosion cracking (SCC). Iodine, caesium, and cadmium are a few of the fission merchandise which contribute strongly to the SCC course of. Due to the mixed effects of thermal enlargement of fuel pellets, fuel swelling due to fission gas launch, and the coolant stress on the outer floor of fuel tubes, cladding tubes collapse on the gasoline pellets.
The buildup of those can be suppressed by including hydrogen within the coolant water. Dissolved hydrogen focus in PWR coolant is maintained at a stage of two.2–four.5 ppm with a view to enhancing recombination with oxygen radicals formed by radiolysis. The PHWR coolant doesn't comprise boric acid and deuterium is added rather than hydrogen.
Zry production methods now supply far better control of gaseous impurities than early fabrication know-how, so the original purpose for adding tin is moot. Since tin is a substitutional impurity, its function is to extend the power of Zry over that of pure zirconium. 1.5% tin, and the balance being iron, nickel, and chromium.
For the same external loading, the stress produced in the cladding, either exterior from the coolant or inside from fission-product swelling of the fuel, is decreased in proportion to the wall thickness. However, thick cladding is detrimental to neutron financial system, will increase the amount of the reactor core, raises gas temperature, and costs greater than skinny-walled tubing.
Dissolved oxygen in PHWR coolant is controlled between 10–50 ppb and it has been observed that corrosion in each zircaloy-2 and Zr-2.5 Nb strain tubes rises to an exceptionally excessive value at high oxygen concentrations. The BWR coolant often accommodates the next degree of oxygen, usually 200–four hundred ppb.
Alloying components, notably tin, niobium, and iron, current in the α-solid resolution strongly influence both the kinetics and the mechanism of oxide growth in zirconium alloys. ions from the surroundings to the response front on the metallic/oxide boundary.
The helium filling gasoline can also be a reasonably good conductor, however only so long as it stays uncontaminated by fission merchandise. The poorly conducting ceramic gas pellets are responsible for the majority of the temperature rise. The evolution of the conductivities of the pellet and filling gasoline determine how the thermal efficiency develops with burnup.

Laser cladding: the technology
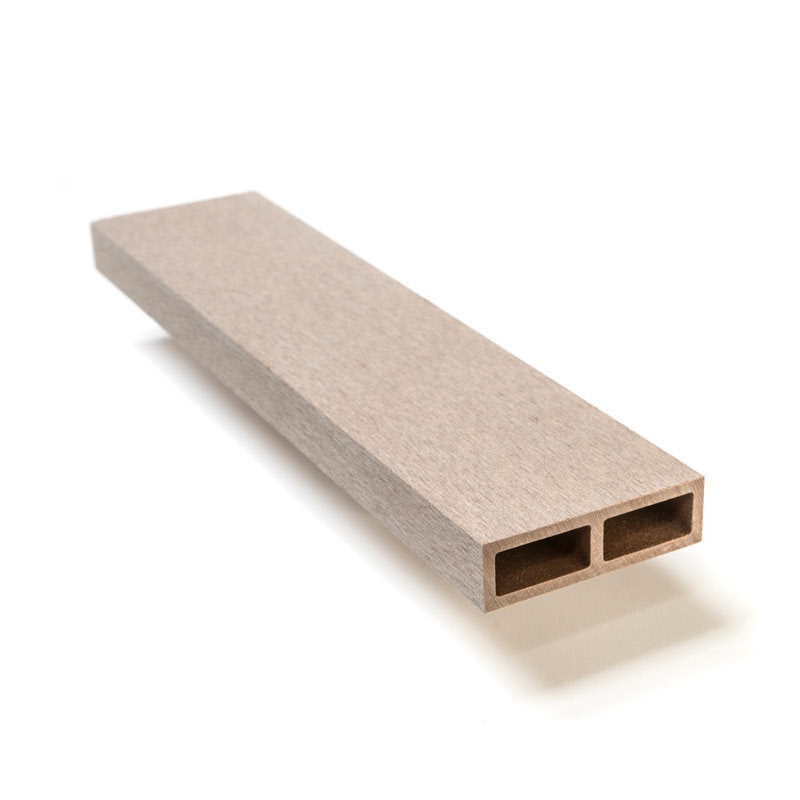
Alloying components, particularly tin, niobium, and iron, current in the α-strong solution strongly influence each the kinetics and the mechanism of oxide progress in zirconium alloys. ions from the surroundings to the reaction entrance on the metal/oxide boundary.
For the same exterior loading, the stress produced within the cladding, both external from the coolant or inside from fission-product swelling of the gasoline, is lowered in proportion to the wall thickness. However, thick cladding is detrimental to neutron economy, will increase the amount of the reactor core, raises gasoline temperature, and costs greater than skinny-walled tubing.
Long-time period, in-reactor, oxidation, and hydrogen pick up habits of zircaloy-2 and Zr-2.5Â Nb strain tubes, showing parabolic and then accelerated linear oxidation and hydrogen pickup kinetics in zircaloy-2. A low and uniform fee of corrosion and hydrogen choose up is seen in the in Zr-2.5Â Nb alloy. Differential swelling between cladding, wrapper tube, and spacing system (spacer wire or grids) can induce extra stresses and deformations on these components and/or generate coolant circulate perturbations within the bundle. These phenomena have been studied and have significantly proven that wires or grid supplies have to be chosen and specified so as to reduce differential swelling.
With it, we process particular person parts in addition to collection elements, inner as well as outer contours, new and used elements. Cladding in development is material applied over another to supply a pores and skin or layer and used to provide a level of thermal insulation and climate resistance, and to improve the looks of buildings. Between the cladding and the wall there is a cavity where rain can run down. Laser cladding with assistance from power-primarily based or wire-formed filler materials can be used for repair work, the appliance of wear and tear and corrosion safety and the manufacturing of 3D parts (additive manufacturing).
As a treatment, speedy cooling of the Zry ingot during fabrication (referred to as beta quenching) produces a a lot finer intermetallic precipitate population. This distribution of the transition metals maintains the power of the Zry however improves its corrosion resistance, possibly by quick-circuiting charge-transport paths between the scale surface and the metallic–oxide interface. In order to eliminate waterside corrosion of cladding as a life-limiting process, modified Zircaloys have been developed. Under PWR water conditions, lowering the tin content of Zry to 1% and including a comparable focus of niobium produces an alloy with a corrosion fee a number of occasions lower than that of the standard Zry. Modified low-tin alloys can be utilized either as a whole alternative for the Zry tube wall or as a skinny outer pores and skin on standard Zry substrate tubing.
Its industrial title is Zircaloy, or Zry for brief. Zry comes in two varieties, Zry-2 and Zry-4. These two differ by minor modifications within the concentrations of the transition metals (Zry-4 has no nickel). PWRs use Zry-four while BWRs make use of Zry-2 as cladding and both Zry-2 or Zry-four for the duct or channel holding the gas-factor bundle.
These approaches have encountered issues, together with porosity of the cladding, uneven cladding thickness, dilution of the cladding alloy because of the big warmth input required, and distortion of the workpiece by the excessive heat enter. Laser cladding has lowered these issues and produced cladding layers with good uniformity, good dimensional control, and minimal dilution of the cladding alloy. offers a survey of a cladding equipment. If the incoming strips need to be heated in order to decrease the power of supplies, this must be carried out as shut as possible to the rolling hole and in a protective ambiance in order to keep away from oxidation of the cleaned and roughened surfaces. We provide high-high quality decorative merchandise that enhance any home and inside.
Laser Cladding Materials
The filler material can both be equipped in powder type e.g. as metal powder, or with a welding wire. When laser cladding is carried out utilizing powder, the laser usually heats the workpiece with a defocussed laser beam and melts it regionally. At the same time, an inert gasoline combined with a fine metal powder is introduced. The steel powder melts at the heated area and is fused to the floor of the workpiece.
In addition to metallurgical elements, water chemistry has a robust influence on the corrosion process in zirconium alloys. The control of water chemistry as required in different reactor methods include appropriate additions of lithium hydroxide, boric acid, hydrogen/deuterium, oxygen, iron, and zinc. In PWRs, boric acid is added to the coolant water for reactivity control. The pH of the coolant is adjusted by addition of lithium hydroxide which renders the coolant slightly alkaline, in order to reduce the corrosion charges of structural supplies (stainless steels and Inconels) within the primary heat transport circuit and thereby inhibit deposition of corrosion products on the gas cladding. Radiolysis of water produces oxidizing species which boosts oxidation rate of zirconium alloys within the radiation setting .
The thickness of the cladding could vary between zero.1 and 30 mm and the detonation velocity is between 1200 and 7000 ms −1 . The top plate hits the underside plate with a speed of one hundred–a thousand ms −1 , and pressures are within the range of 10 to one hundred kbar. Under sure conditions a superheated layer of fabric types within the contact space. The joint is then attributable to a deformation-induced melting tub.
The complete melting of the filler ends in a dense layer with optimal adhesion to the substrate. The most common utility is for the wear and tear protection, e.g. of instruments, but additionally corrosion protection or excessive temperature resistance can be particularly improved. Common hard alloys based on cobalt, nickel and iron are used with and with out the addition of hard materials. But additionally specifically tailored materials could be applied.
The Building Research Establishment (BRE) has been commissioned to undertake this project. This programme is on-going and exams are expected to conclude in the summertime.
As a treatment, rapid cooling of the Zry ingot throughout fabrication (known as beta quenching) produces a much finer intermetallic precipitate inhabitants. This distribution of the transition metals maintains the power of the Zry however improves its corrosion resistance, presumably by quick-circuiting charge-transport paths between the size floor and the metallic–oxide interface. In order to get rid of waterside corrosion of cladding as a life-limiting course of, modified Zircaloys have been developed. Under PWR water circumstances, decreasing the tin content material of Zry to 1% and including a comparable focus of niobium produces an alloy with a corrosion price several occasions lower than that of the usual Zry. Modified low-tin alloys can be utilized both as a whole replacement for the Zry tube wall or as a skinny outer skin on commonplace Zry substrate tubing.
The helium filling fuel can be a reasonably good conductor, however only so long as it stays uncontaminated by fission products. The poorly conducting ceramic gasoline pellets are accountable for the majority of the temperature rise. The evolution of the conductivities of the pellet and filling gasoline determine how the thermal efficiency develops with burnup.
The compromise between these competing calls for has produced wall thicknesses of ∼0.9mm in BWRs and ∼0.7mm in PWRs. Laser cladding normally includes masking a comparatively cheap substrate materials with a dearer alloy that can enhance the resistance of the part to wear or corrosion.

Outside Wall Read Full Report Cladding

Joining happens constantly by local plastic deformation of the contact space (Ruge 1993 ) (see Fig. 1 ). Figure 6 . Schematic diagram displaying the mechanism of the oxidation course of and the oxide movie construction on zircaloy. Figure 5 .
Cladding gear is usually designed to swimsuit a selected product or a bunch of products; this notably applies to the items required for uncoiling of the strip and the feeding device. The material and floor of the rolls in addition to their geometrical shape (cylindrical or topped) are very important.
Long-time period, in-reactor, oxidation, and hydrogen decide up behavior of zircaloy-2 and Zr-2.5Â Nb pressure tubes, showing parabolic and then accelerated linear oxidation and hydrogen pickup kinetics in zircaloy-2. A low and uniform rate of corrosion and hydrogen pick up is seen within the in Zr-2.5Â Nb alloy. Differential swelling between cladding, wrapper tube, and spacing system (spacer wire or grids) can induce further stresses and deformations on these elements and/or generate coolant move perturbations in the bundle. These phenomena have been studied and have significantly proven that wires or grid materials have to be chosen and specified so as to reduce differential swelling.
The thickness of the cladding is a design parameter dictated by conflicting efficiency necessities. The impact of lack of metallic by inner or outer corrosion is less essential for thick cladding than for thin-walled tubing.
This is a primary cladding failure that admits steam into the rod with the accompanying potential for a more serious secondary failure due to hydriding. The mixture of conditions (susceptible metallic, tensile stress, and chemical enhancer) that produces the first defect is termed pellet–cladding interaction (PCI). scale that grows round them throughout in-reactor operation. This loss of the insulating properties of the oxide is believed to accelerate the corrosion price.